Personalised Leather Guitar Strap
- Peter Smith
- Feb 21, 2022
- 4 min read
Updated: Jul 7, 2023
I love making a personalised leather guitar strap.
Whilst they are not a complicated item to make (i.e. not necessarily advanced leather craft) they still take 3 days to make. There are over 600 stitches holding the top layer firmly onto the main strap and it takes a day to complete the dyeing, especially when shading and contrast is needed.
Personalised Leather Guitar Strap, how I make them
The materials
My straps are made from vegetable tanned 2mm tooling shoulder, which is a softer leather but strong and yields beautifully to the stamping tools.
It also takes dye nicely, allowing me to add shading to my colours. Of course, the softer the better for comfort.
I use solid cast hardware, made in a foundry in the UK.
The tread I use is known as 'Tiger Thread', and it's a thick one of this job at 1mm for aesthetics. I like to use complimentary or contrasting thread colours, depending on my design at the time.
The commission
Naturally, the first thing I need to understand is exactly what the client wants. We chat and discuss options and often clients are open to added or new ideas to the project.
This guitar strap was commissioned for a 45th birthday present. Ahh, first thing to note, a special occasion.
The client also wanted a name put on. Point number 2 - personalisation.
He also knows that the recipient is into dragons and fantasy type characters and likes dragons. Point number 3, additional design work.
It was decided that the underlining is to be shearling (10mm hair length) for comfort and that bit of luxury - it is a special birthday gift indeed.
The hardware was chosen from my stock is silver plated american three piece buckle, loop and tip.
And of course the colours were broadly 'red'.
Preparation
I knew the length required, since the customer is the same height as me and plays an acoustic guitar - so an acoustic guitar strap is required at 46".
The under strap is a full 2.5" wide and the top strap is 1.5" wide.
The design
Knowing the colour choice to be red, I had a lot of choice for complementary colour mix and shading.
I designed the '45' inside a circle, which would be tooled right in the middle of the strap.
Next came the Celtic love knot with integrated dragon and treble clef design to go on the back of the strap, all sketched by me.
The name is to go on the front and font choice was also given to me by the client.
I sketch my design with coloured pencil and the client approves - oh goodie, this is an exciting job! I could not wait to see the finished personalised guitar strap!
The making
Preparation
After measuring and cutting the leather components for this guitar strap (top strap, bottom strap, underlining and tail with buckle) the components are marked for stitching, button holes, buckle holes, crew hole, slots for the plectrums and a hole for the tassels.
I also cut the tassels (I make my own lace for this).
The button, buckle and crew holes, plectrum and tassel holes are cut and the edges are burnished.
Tooling
After tracing the patterns onto the leather, I tool the designs, starting with the 45 in a circle, right in the centre of the top strap.
Next I tooled the integrated love knot / dragon / treble clef design.
Lastly I tooled the name 'Roksana' in the style requested.
Colouring
So this is where my personality comes in. Working with red as the base colour, I used shades of red and brown. These colours will show off the tooled work nicley.
On the top strap, I wanted a darker base so that the tooled designs would stand out with the brighter colours. So, darker reds and browns on the top strap. I wanted the entire top strap to pop, so I went with lighter shades of red and brown than I did on the top strap.
The 45 and treble clef are the lightest colours, so let's dye those first in yellows.
Working from lightest to darkest, I dye the tooling. Once all that is done, I get on with the rest of the strap.
The top strap goes from dark red into chocolate browns, varied to give me a slight marbled colour effect. I dye around the design work, being careful not to run into the tooled work.
The tassels and tail are also dyed.
Assembly
Now comes the next level of skill - stitching. In my guitar strap designs I use a 1mm punch for the stitch holes (as opposed to the traditional stitching awl). I do this for a point of difference from any other guitar strap and to provide me with a different look to stitching.
So, punch out the holes and start hand stitching - all 600 or so stitches. In this case, I used a dark brown thread to blend with the dark edges on the top strap and used the traditional saddle stitch.
The buckle and loop are stitched on the tail next.
I make up the tassel bunch and insert them into the hole waiting for them in such a way that they will not come out.
I can finally put the underlayer on - the shearling. It looks like a simple enough job, however, it's really difficult to cut it exact. Shearling stretches and misbehaves when working with it. So, I glue the backing on over sized. Once bonded, I then cut the shearling along the edges of the guitar strap. But, it's not just 'get a pair of scissors or knife and trim off the excess' kind of job. If you do that, you will end up with the edges of the shearling with uneven or short hair. I cut using a scalpel, and only cut the actual skin, being careful not to go deep so as to cut the hair.
Finishing
Any leather article I make, including guitar straps, transform during the finishing process. I have my ways, which I learned and developed many years ago and will remain my secret!
Suffice to say that the guitar strap pops and shines when it is finished as well as being protected.
The shearling is brushed through before I package the guitar strap for the customer.
This was a great pleasure to do and I can say that the client was very pleased with it. He even recommended one of his fellow musicians to me.
There is no end to designs, let the imagination go, as you will see here. These are fun and a pleasure to make.
If you want that special, personalised, bespoke guitar strap, talk to me, it will be my honour and my pleasure to make it for you.
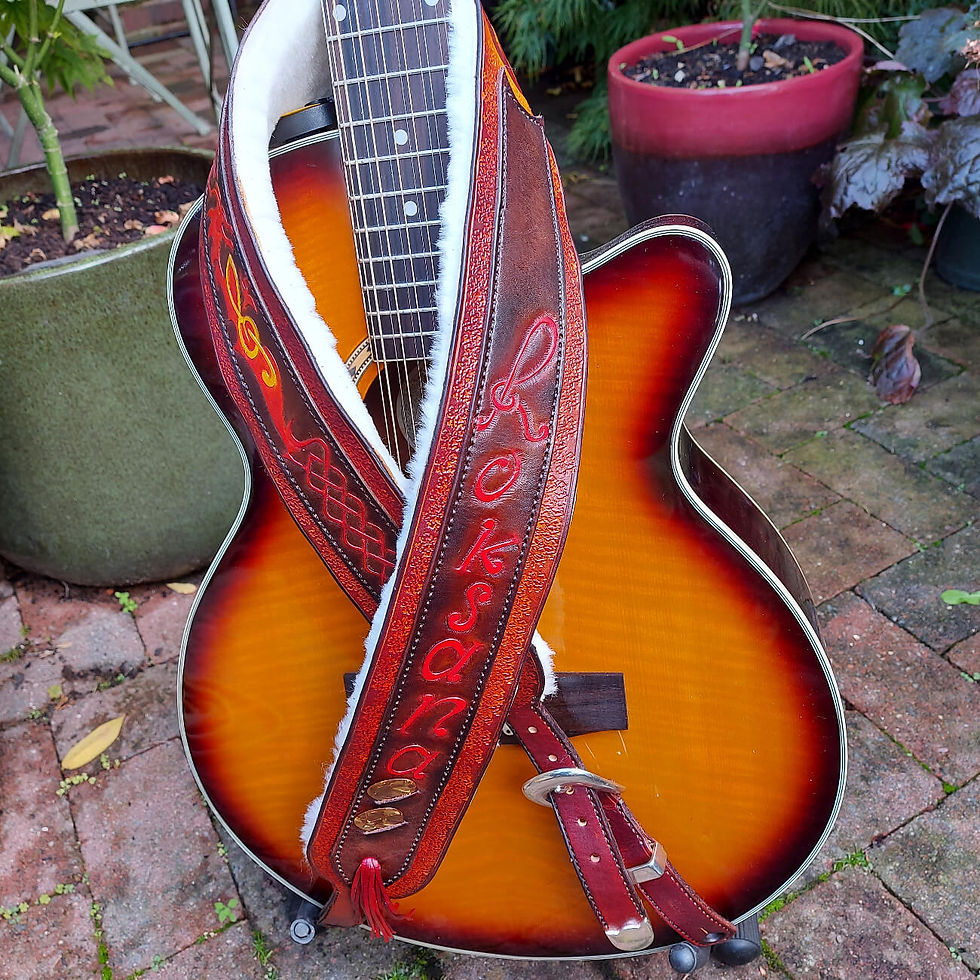



Comments